Industry 4.0
What is Industry 4.0 and the fourth industrial revolution?
Industry 4.0 refers to the fourth industrial revolution and the cyber-physical transformation of manufacturing. The name is inspired by Germany's Industrie 4.0, a government initiative to promote connected manufacturing and the digital convergence of industry, businesses and other processes.
Industry 4.0 encompasses a long and evolving list of technologies. While it can be defined in simple terms, the number of systems and tools that fall into this category tends to be in flux.
Among these technologies are robotics, artificial intelligence (AI), internet of things (IoT) and automation. Industry 4.0 is also referred to as smart manufacturing because these technologies are deployed to assist in manufacturing and industrial production line settings. However, Industry 4.0 has other real-world use cases such as supply chain management, logistics, warehousing and cybersecurity.
History and evolution of Industry 4.0
The first industrial revolution took place at the end of the 18th century when steam and waterpower made mechanization possible. Locomotives are a good example of how steam power transformed transportation.
The second industrial revolution occurred at the start of the 20th century with the advent of electricity, which made assembly lines, mass production and division of labor possible. The third industrial revolution was at the start of the 1970s, when the use of computers and digitization made it possible to further automate machines and production processes.
The fourth industrial revolution might best be described as an extension of the third revolution. Industry 3.0 introduced computers into the manufacturing process, and Industry 4.0 is focused on connecting those computers to one another. However, Industry 4.0 goes beyond getting systems on the factory floor to communicate. When fully applied, it provides functionality that enables smart factories and digital manufacturing.
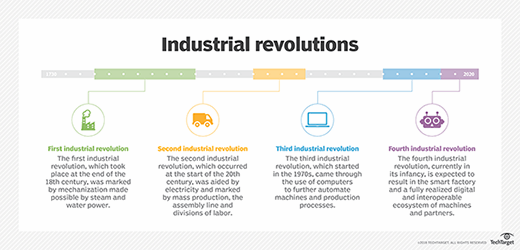
Industry 4.0 and IoT
IoT technologies are a key part of Industry 4.0 and a major trend of the last decade. IoT is the ability to connect nontraditional computing devices to the internet or private networks.
IoT often refers to smart, connected, consumer devices, such as internet-connected thermostats and appliances. However, manufacturers have also adopted the concept and have deployed large numbers of connected smart sensors in factories and other industrial facilities. The use of such sensors is referred to as the industrial internet of things (IIoT).
IIoT is a key enabler of Industry 4.0, but it commonly uses other connected technologies, such as smart machines and cyber-physical systems. All these systems work together to achieve new levels of automation.
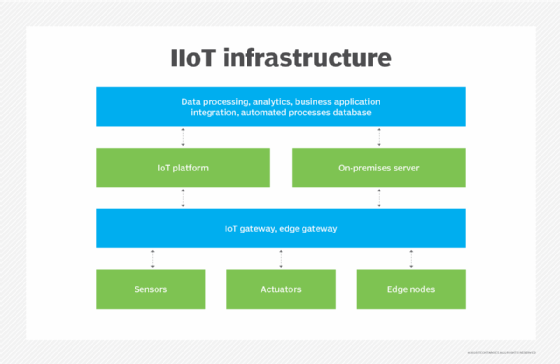
What are the applications of Industry 4.0?
Industry 4.0 can be applied to all levels of the manufacturing process from product development to product end of life. Specific use cases of these technologies include the following:
- Predictive maintenance of crucial equipment. IIoT sensors integrated with industrial equipment used for production lines and utilities can monitor performance and detect anomalies that indicate maintenance and updates are needed.
- Real-time data collection and analysis. IIoT devices transmit real-time data to AI and machine learning platforms where it's analyzed to identify any potential threats or failures as well as opportunities for improving efficiency. Factories equipped to analyze large amounts of data and use it to make automated decisions are known as smart factories.
- Supply chain visibility. Long-distance tracking of goods as they move through a supply chain can be achieved with physical devices, cloud computing for data transmittal and storage and software dashboards that give workers the information they need. Industry 4.0 also makes it easier to source raw materials used in manufacturing a product.
- Additive and digital manufacturing. Additive manufacturing, also known as 3D printing, can improve prototyping, customization and other aspects of manufacturing new products. Workers can digitally modify them and add details as needed.
- Inventory management. AI and machine learning can ingest data on product purchases to make predictions on what inventory customers will need, optimizing inventory management. This mitigates delays and improves the customer experience.
- Augmented reality. Augmented reality devices provide data and instructions to workers from remote locations to help them operate wherever they are in a facility. Also, it enhances training for new hires through simulations of real-world scenarios.
- Sustainability. Industry 4.0 tech can help regulate power consumption, identify ways to reduce pollution emitted from machinery and monitor physical assets that provide sustainable energy.
Industry 4.0 and sustainability
Industry 4.0 can play a key role in making factories and plants more sustainable. For example, IIoT sensors and the IT networks they operate on can monitor power use so the machinery used at a particular site can reduce power consumption. Also, AI and machine learning algorithms can analyze data on resource use at a given site to identify opportunities for improving operational efficiency.
Industry 4.0 technologies not only monitor traditional manufacturing systems but can also monitor sustainable energy sources, such as wind, solar and hydroelectric power generation, to aid sustainability efforts. In these types of systems, distributed IoT devices are situated in remote locations where they are used to provide information on predictive maintenance and other issues for the renewable energy sources. The devices can use the data they collect to make maintenance decisions in some cases, and in others, they transmit the data to workers who make decisions based on the data.
What technologies are driving Industry 4.0?
The convergence of various technologies is driving Industry 4.0, including the following:
- IIoT and the use of sensors.
- Big data and predictive analytics.
- AI and machine learning.
- Low-power wide area networks for machine-to-machine and IoT networks.
- IT/OT convergence.
- Touch and voice interfaces and augmented reality systems.
- Advanced robotics.
- 3D printing and additive manufacturing.
- Cloud computing.
Essentially, all these new technologies were created for humans to interact with machines, for machines to communicate with each other and to achieve more complicated goals. They also enable data to inform and optimize all manufacturing processes and lead to more interconnected processes, ranging from design through the end of the product lifecycle.
What are the benefits of Industry 4.0?
Industry 4.0 provides numerous benefits to organizations that choose to implement it. They include the following:
- Increased visibility of processes. For example, Industry 4.0 concepts can enable original equipment manufacturers to see how customers use a product versus how it is expected to be used.
- Enhanced monitoring of machinery. Sensor data can help an organization monitor a manufacturing process in real time. This data can then be compared against a digital twin -- a simulation that runs at perfect efficiency -- to determine where the process could be improved.
- Advanced training. Some organizations have applied Industry 4.0 concepts to employee training. These training programs use augmented reality to teach employees how to operate machinery and how to avoid unsafe practices before the employee is ever allowed on the factory floor. Augmented reality-based training is used in areas such as fire suppression and first aid as well.
- Avoiding downtime. Prior to the adoption of Industry 4.0, industrial machinery was serviced based on manufacturer recommendations. However, with Industry 4.0 technology, machinery equipped with sensors can monitor factory machinery's health on an ongoing basis. This enables organizations to anticipate problems before they occur and proactively take corrective action. In some cases, machines can even automatically place an order for replacement parts when needed. All this together can help an organization avoid costly outages that disrupt the manufacturing process and cause downtime.
- Increased productivity. Digital technology used on the factory floor is tied to back-end corporate data systems, enabling big data analytics to be performed on data associated with the manufacturing process. Such advanced analytics can help the organization spot trends and gain insights that help it become more productive and profitable.
- Reduced costs. Industry 4.0 tech can detect and prevent issues such as equipment failures and excessive resource use, and potentially reduce costs.
What are the challenges of Industry 4.0?
There are also challenges for organizations adopting Industry 4.0 tech. They include the following:
- Cost. The upfront costs of purchasing and implementing industry 4.0 software and physical assets can be burdensome, particularly for small and midsize businesses.
- Interoperability. Early on, one of the main challenges for organizations wishing to implement Industry 4.0 was interoperability. The machines and sensors on the factory floor often used different protocols, making communication between connected devices difficult. However, standards have emerged as Industry 4.0 sees greater adoption.
- Security. In the past, the factory floor systems tended to be proprietary, and it was rare for such systems to be connected to one another or to back-end IT systems. The vendors that created these systems rarely took a security-first approach to their development efforts. However, connectivity between devices and IT resources can expose these devices to the same cyberattacks that have long plagued traditional IT devices. Additionally, a compromised IT system can provide an attacker with a path through which to attack the resources used on the factory floor.
- Configuration complexities. Misconfiguring networks and devices leads to faulty or nonfunctional processes. Configuring everything correctly can be a complex process and requires skilled employees to handle.
- Disruptions. These can occur for many reasons, including cybersecurity threats, equipment failures and natural disasters. Industry 4.0 technology is just as vulnerable to these issues as earlier technology.
The future of Industry 4.0
Industry 4.0 is a slowly evolving digital revolution. Many organizations have begun to use these technologies, but others are hesitating for reasons ranging from cost to uncertainty about value. As the efficiencies and benefits of these technologies become apparent, more businesses will adopt them.
It will take time to overcome obstacles associated with Industry 4.0, such as upskilling needs, so employees can properly use these tools and systems. The rise of AI and machine learning into the mainstream is a prime example of how disruptive Industry 4.0 tech can be to a business model. For example, workers who were previously tasked with analyzing large data sets -- in markets such as healthcare, retail and manufacturing -- can be replaced by machine learning algorithms that provide insights and predictions.
Some industry experts are discussing Industry 5.0. It's less focused on digital transformation and economic growth in the manufacturing industry and more about enabling people and machines to operate side by side in the most effective ways possible for the well-being of human workers. This is a more distant reality, as the world is currently in the early stages of Industry 4.0. Still, the goal is to have machines handle automated processes so people can focus on other issues, such as product innovation, cybersecurity, climate challenges and sustainability. It remains to be seen when this vision will become reality and how many businesses will achieve it.
AI and IoT are key parts of the Industry 4.0 ecosystem and the possibilities that exist for the two functioning together are endless. Explore different ways in which AI and IoT technologies work together and how AI supercharges existing IoT systems.