Flint, MI—Flint may soon be home to a unique, potential solution for Michigan’s dearth of affordable housing: a 3D-printed home.
While the Flint & Genesee Economic Alliance and a host of partner organizations are still sorting out the project’s final budget and timeline, a $116,500 grant from the Michigan Economic Development Corporation has set the process of building the region’s first 3D-printed house in motion.
“When we got the opportunity to bid on a regional grant, we said ‘enough of the studies, let’s print a house,'” said Tyler Rossmaessler, Executive Director of the Flint & Genesee Economic Alliance.
The concept of 3D printing as a home-building technique was relatively new at the time Flint’s “prosperity region” (a grouping of counties designated by MEDC to best leverage resources across the state) applied for the grant. But, said Rossmaessler, the group saw the potential of the building technique and viewed the grant as an opportunity to explore the innovative route toward more affordable housing in their region.
“Housing has so many facets to the local economy,” said Rossmaessler. “How do we help our businesses get people (hired), but the people don’t have anywhere to live? The sustainability of the place—and so many kinds of things—are wrapped up into housing, which is why we were all interested to focus on it.”
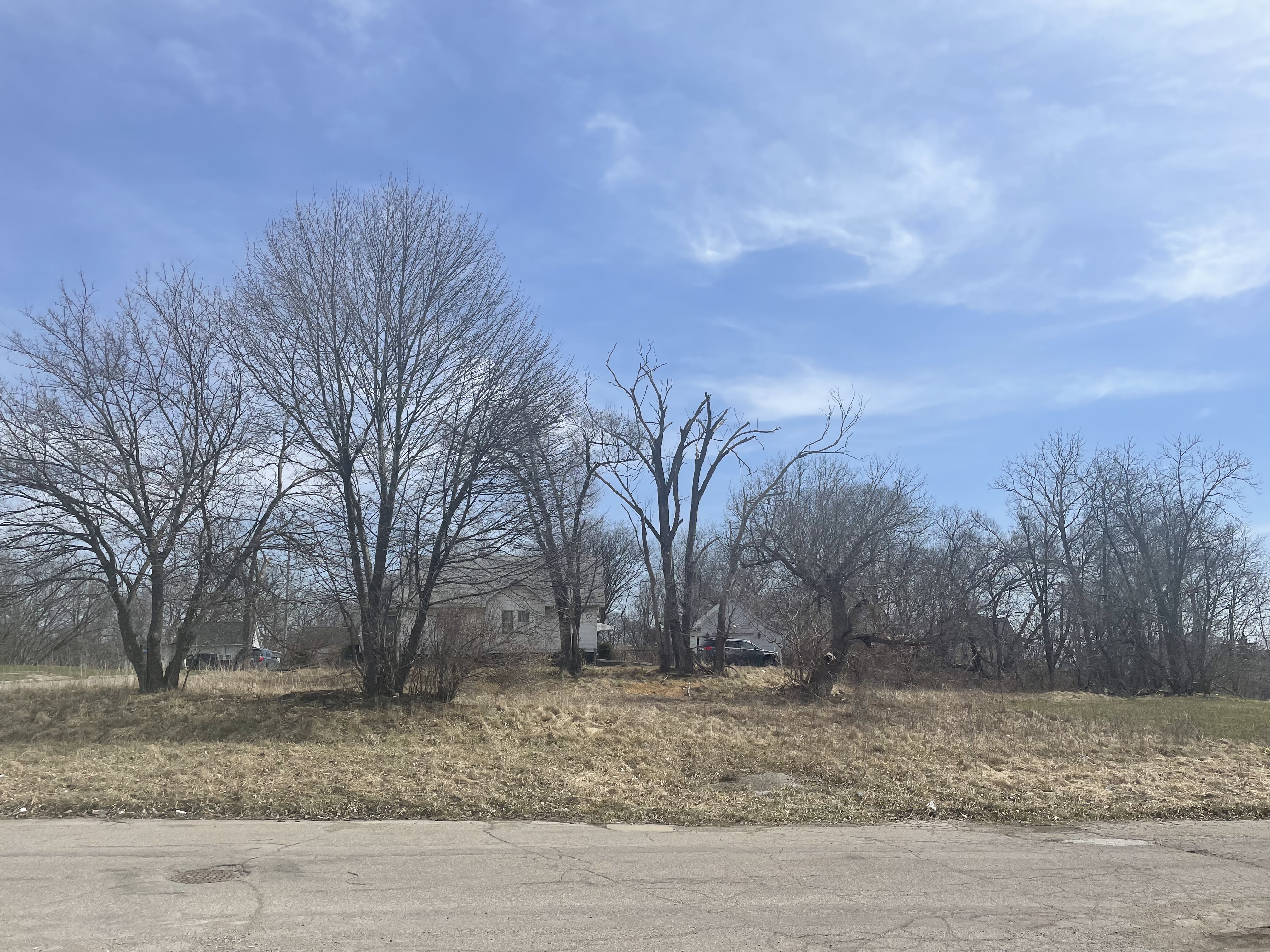
The problem of creating quality, affordable housing that makes financial sense for investors is not new to Flint.
Flint Beat has reported on multiple entities working to build or renovate the city’s housing stock for such purposes, such as Uptown Redevelopment Corporation’s coming Carriage Town development and Communities First Inc.’s work at Georgia Manor and on University Avenue.
But, as Rossmaessler pointed out, the challenge for those entities—and any potential developers or individuals looking to build a home in Flint—is that the cost to do such work is consistently higher than they stand to make back.
“The city of Flint has its kind of nuances to their housing troubles and a more rural part (of our prosperity region) up in the thumb would have their own nuances,” Rossmaessler said. “But at the end of the day, it’s the same problem: it’s hard to build a house for what it can sell for.”
So, Flint’s prosperity region stakeholders agreed to ask for grant money to build two 3D-printed houses, Rossmaessler said, one in an urban area and one in a rural area, to see if the homes could be a more cost-effective solution to the region’s affordable housing shortage.
“Let’s see if this can lower the cost of construction,” Rossmaessler said of the group’s rationale. “Maybe 3D houses can be that gap between what it takes to create and build a house and what it can sell for.”
Ultimately, MEDC awarded the region grant money for only one such home, and the stakeholders chose Flint for its urban location.
Now, a team of local organizations, contractors, and architects is being assembled to make the project happen, though it remains uncertain whether the 3D home will be the affordable housing solution they hope it to be.
‘What the heck is a printed house?’
To learn more about the process of building a 3D-printed home, the Flint & Genesee Alliance took a tour of Citizen Robotics, a Detroit-based robotic construction nonprofit, and a subcontractor for Flint’s own project, in late February 2022.
“One of the things that I talk about when I’m talking about 3D-printing is that it’s an innovation that lets you replace stick framing,” said Tom Woodman, founder of Citizen Robotics, referring to the traditional method of building a home, piece-by-piece, on its intended site.
Woodman talked about the advantages of Citizen Robotics’ method, namely less labor (a robot ‘builds’ by layering concrete according to a computer input instead of dozens of men framing and drywalling on-site) and less time: depending on the dry time and scale of a project, the printing process can take mere days to weeks instead of months or years.
And, because the building material basically concrete, Woodman added, “you’re building with something that isn’t going to rock, it’s termite resistant, and it’s hard to blow it down: just ask the Three Little Pigs.”
The group laughed as Woodman continued explaining the advantages of the 3D-printing process in home construction.

Normally, he said, one small change on a traditional home build—like a window being moved a foot to the left—means contacting architects for new blueprints, communicating the change with an onsite contractor, and hoping the contractor sees to it the change is made by their construction team.
“Well, in the world of 3D printing, you just change that in the 3D model, and it literally is a five to 10-minute change,” Woodman said.
Woodman walked over to a computer monitor near the space’s giant robot arm. “You send that print back through a slicing algorithm”—he paused, pointing to the screen—“and then feed it directly to the robot. And the robot is going to spit out that changed thing. So much less opportunity for human error, and much less opportunity for miscommunication along the way.”
One tour member said she was mildly familiar with 3D printing and thought a 3D house might be made of plastic, a common material for 3D printing hobbyists making figurines or housewares on their home printers.
Woodman said that Citizen Robotics’ robot works in much the same way: building segments of each home layer by layer, but on a much larger scale and using Laticrete, a concrete-like material, instead of plastic.
Woodman explained that the materials used in 3D printing construction methods mean homes start air-tight in a way that cannot be achieved with a stick-built method. In the long run, the concrete structures save occupants money on heating and cooling bills. In the short term, it also means fewer materials are needed for construction as builders do not need to worry about protecting concrete from weather extremes during buildout like they do with traditional wood framing.
Woodman ended the tour by showing the group a small-scale segment of a 3D-printed home, noting some elements—like its roof and windows—would not be 3D printed and highlighting customization options like patterns, paint, and stucco.
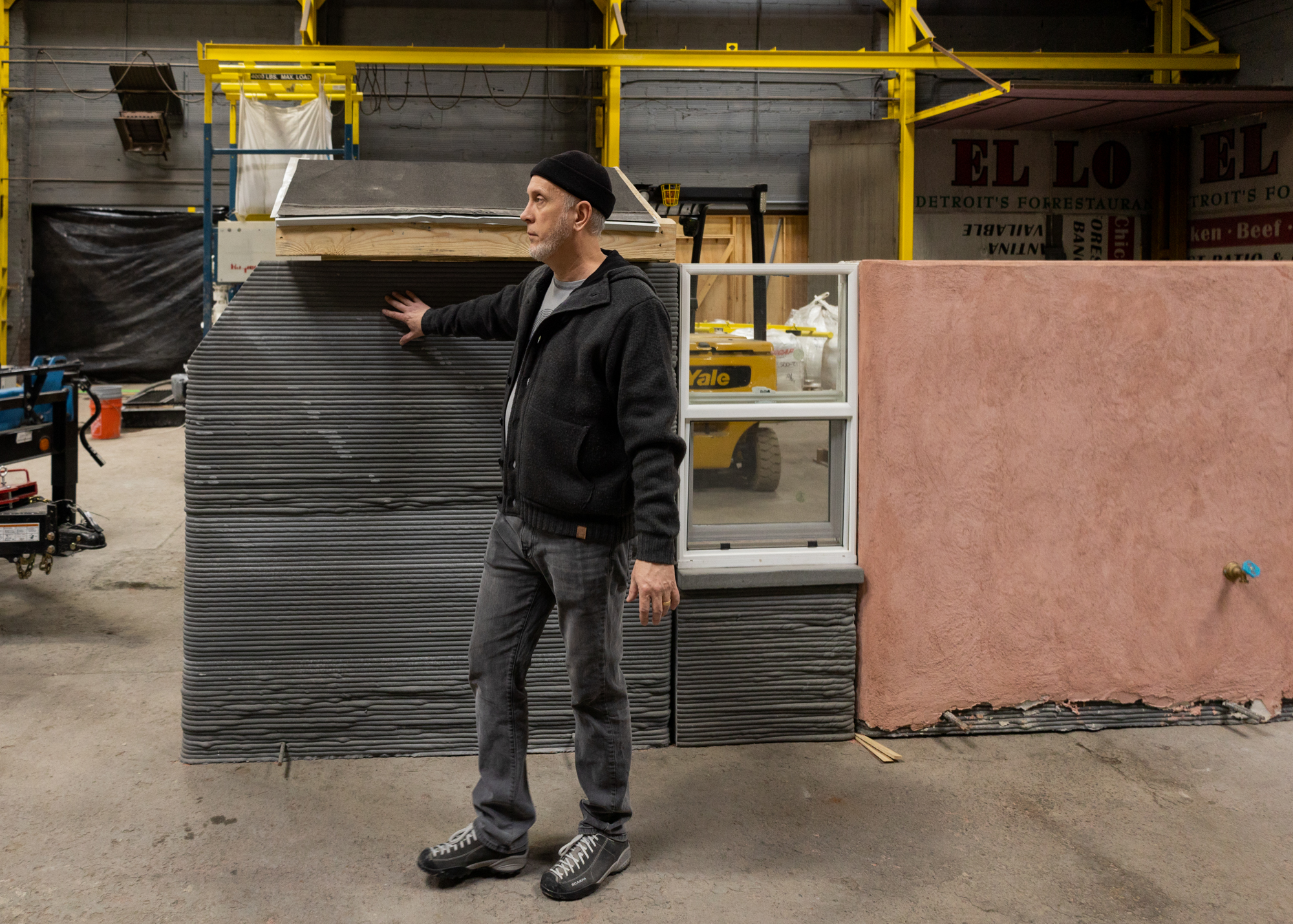
“Yeah. What the heck is a printed house?” Rossmaessler later joked about how he’d originally approached the tour. “Is it plastic? Is it ugly? We’ve got to understand if people want to live in printed houses, too. It’s a viable technology, and it can lower the cost (to build). But if people don’t want it? That doesn’t fix the problem.”
But so far, it seems like people do want it.
In 2021, multiple 3D-printed projects began or were completed across the country: one in Virginia, a couple in Arizona, a whole 3D-printed neighborhood development in Texas, and more. On the tour, impressed visitors began framing questions as if they were planning to buy a 3D home themselves.
“Okay, so I have a queen bed, and I want to move this outlet over here…” one woman could be heard asking Woodman as the tour group began to depart.
But while developers and homebuyers are beginning to embrace the new tech, it still has its limitations, especially when it comes to Flint’s intended goal for it: affordability.
Current Limitations
While part of Citizen Robotics’ mission is to “reduce the cost of housing construction through the adoption of robotic construction techniques,” Woodman is the first to admit they aren’t there yet.
“Here’s the thing, we think we’re going to put that house up at par with conventional construction,” Woodman said, pointing to a rendering of a home for another site. “But think about it. Stick-building has been around for literally 1,000 years, and when it’s a mature industry, we’ve kind of reached the end of our ability to make it less expensive. But here, we’re at the beginning of our innovation curve.”
Woodman said he expects costs of robotic home construction will begin to go down as Citizen Robotics and other such organizations refine their printing processes and material expenses decrease in tandem with more people and products joining the industry.
“Thirty years ago, we could print with one thing: just plastics. A special kind of plastic. Today, we can print with dozens and dozens of things,” he said, citing metal and ceramics. “And the same thing is going to happen here.”
Given that the costs of robotic construction are still relatively equal to standard construction for now, Flint’s 3D-printed home will most likely not be fully funded by MEDC.
“The grant can’t pay for the whole thing,” Rossmaessler said.
According to Quicken Loans, the average cost of new-build home construction in Michigan is roughly $225-265k, but costs can vary greatly depending on “features, the land, neighborhood, building materials, design and more.”
Rossmaessler said that his team is working with the Genesee County Land Bank, which owns the currently vacant site of the future house, and Flint’s Local Initiative Support Corporation, or LISC Flint, on financing the rest of the project.
“We’re trying to do it around $200 per square foot…but we don’t have the design yet,” he said.
And that design is crucial since it will determine the final cost for the home.
Rossmaessler said the design will come after stakeholders decide on the “persona” for whom the 3D-printed house will be built.
“It starts with, who are we designing this for?” he explained. “For example, I am in my thirties, and I have a wife and three kids. So that’s my persona. If they were designing the house for me, it would look like one thing, versus maybe an empty-nester who’s going to age in place, versus a young professional who doesn’t have a family.”
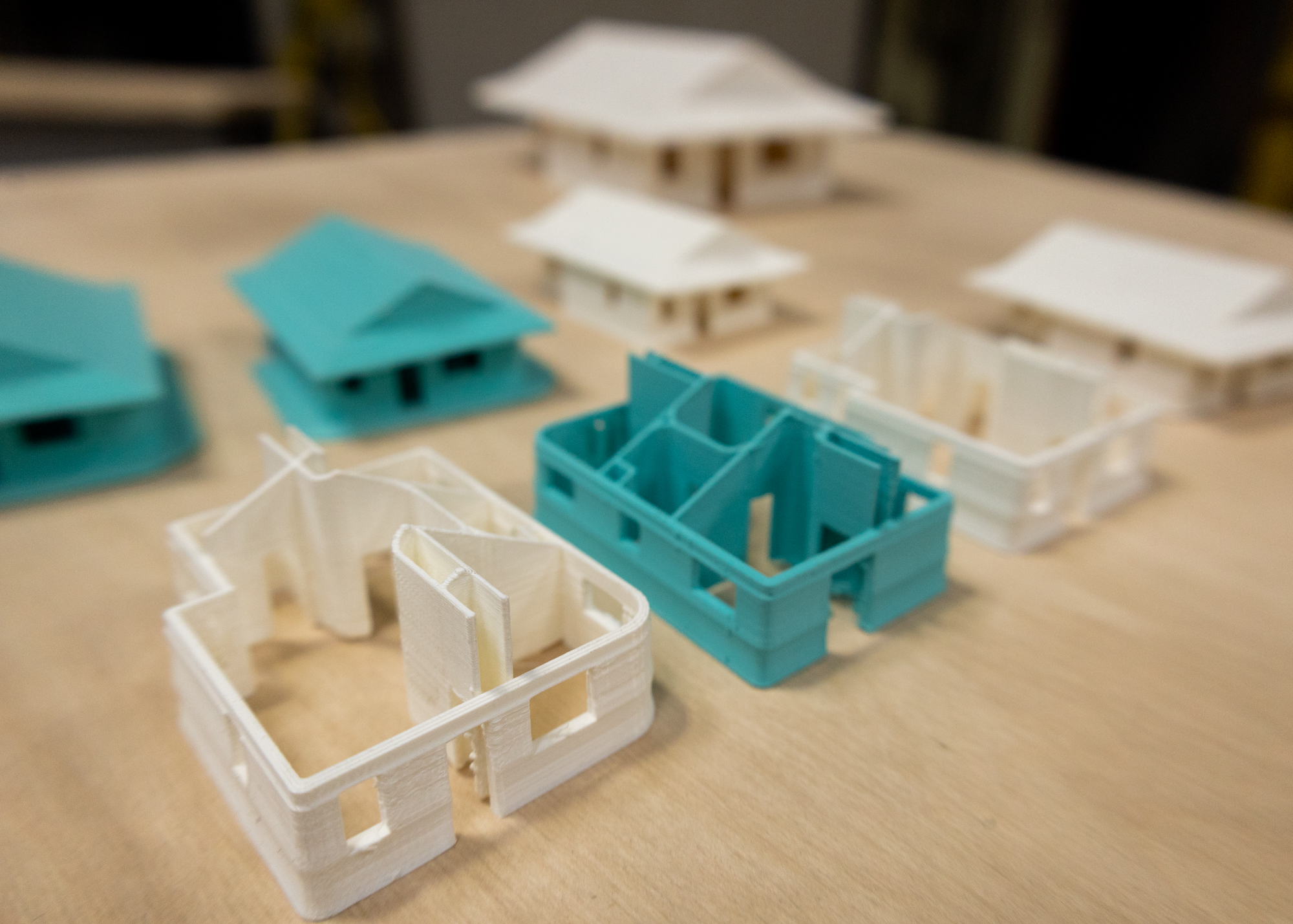
So until the regional stakeholders decide on a persona and design, Rossmaessler said, it remains to be seen whether the budget for the region’s first attempt at affordable 3D home building will be any more tenable than traditional methods.
But, he added, that doesn’t mean this project isn’t a step in the right direction.
As the market for 3D-printed homes grows, the price of materials decreases, and robotic construction gains talent and adopters, Flint could be on the forefront of a key piece of the complex affordable housing puzzle.
“Obviously not everybody’s going to live in a house like this,” Rossmaessler said. “But this is one of the pieces.”
In addition to needing to finalize contractors, a design, and a budget, another potential hurdle comes in the form of building approvals. As Flint has no precedent for this kind of construction, there’s no clear understanding of what that process will take with the city’s planning department as yet.
“That’s why the city of Flint is on this team,” said Rossmaessler. He said he hopes having the city’s economic development department on the project will help the group navigate the planning and permitting process once a design is known.
Further Possibilities
Despite the unknowns and the possibility of potentially netting even on the city’s first 3D-printed home, the project’s many stakeholders remain excited to move forward.
“It’s just innovative and new,” said Juan Zuniga, executive director at LISC Flint, said of the house. “And we hear the conversations and we hear it happening across the country in other cities … To be able to help realize that come to fruition here in Flint? That’s exciting.”
Zuniga’s team is tasked with helping to find financing for whatever costs remain after the MEDC grant money is exhausted for the project. He said he’s optimistic that even if this first project isn’t the fix-all for Flint’s affordable housing needs, it may be part of something else, too.
“It could spur the movement of a whole neighborhood, right? Or multiple blocks in a specific area. And it just allows a different look and feel for housing in Flint.”
For their part, the Citizen Robotics team is also optimistic, recognizing that it will take time for 3D printing to be the affordable housing solution they hope it will become.
“We’ve been calling this a process innovation, not a product innovation,” said Evelyn Woodman, communications director and co-founder of Citizen Robotics, and Tom Woodman’s daughter. “For us, it’s really about bringing in these advanced manufacturing techniques into the built environment.”
The younger Woodman noted that using robots for manufacturing has reduced the costs of many other day-to-day products in our world, like clothing and electronics. “So being able to bring that into the housing space we think is really important and something that could have happened a long time ago,” she said.
But, she and her father agreed, robotic construction cannot solve the state’s dearth of affordable housing on its own.
“We know that this is not going to be the only solution to the affordable housing crisis,” she said. “So we also care about bringing in alternative financing models to help people afford their homes long term and build equity.”
“This little lever for change that is 3D printing might be something that could create a tipping point,” the elder Woodman added. “We have outsized impact just because of this crazy 3D printer. Just because you’ve got a robot, people are paying attention.”
He said he hopes to harness that attention to drive awareness to the affordable housing discussion, to attract younger people to the trades, and to start making real strides in the affordable housing space as a collective.
“We have to use this opportunity to talk about what else is needed because the solutions are there,” Woodman said. “We just have to pull the right set of things together that create cohesion, and then move forward with that.”
Rossmeassler said that the many parties involved in creating the home have a “notional agreement” that is solidifying before they head into the project’s design and permitting phase. He said that while they do want to move forward quickly, there is no precedent for this type of construction in Flint, so he was reluctant to try to give a firm timeline for the build-out.
“I’m excited about this from so many levels,” he concluded. “Number one: to solve the housing problems in our communities, we have to explore and experiment if this is possible. … Number two, show the world that Flint does cool things. … Number three, I think people want to live in the city of Flint. I believe there is demand. People want to be there. And we’ve just got to provide more quality, affordable homes.”